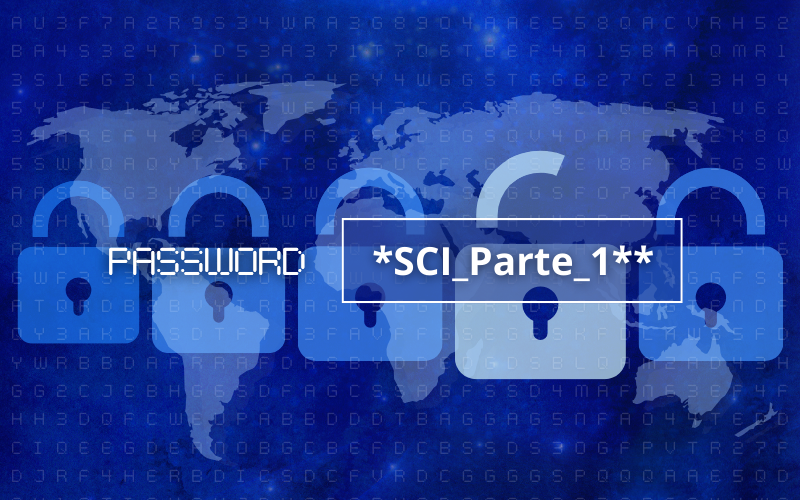
The Initial Access tactic is one of the 12 tactics that make up the matrix developed by MITRE for industrial environments (for more information on the matrix, feel free to consult the article ICS Matrix, the State of v11). Within this tactic, different techniques used by attackers with the aim of gaining unauthorized access to an industrial environment are shown. This is often the first target of external attackers, as access to the ICS's internal environment allows internal computers to be recognized and exploited, move around the network, gain elevated privileges, or steal sensitive information. Therefore, it is important to know this tactic in order to defend our systems
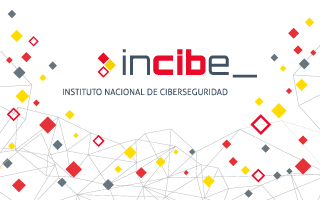
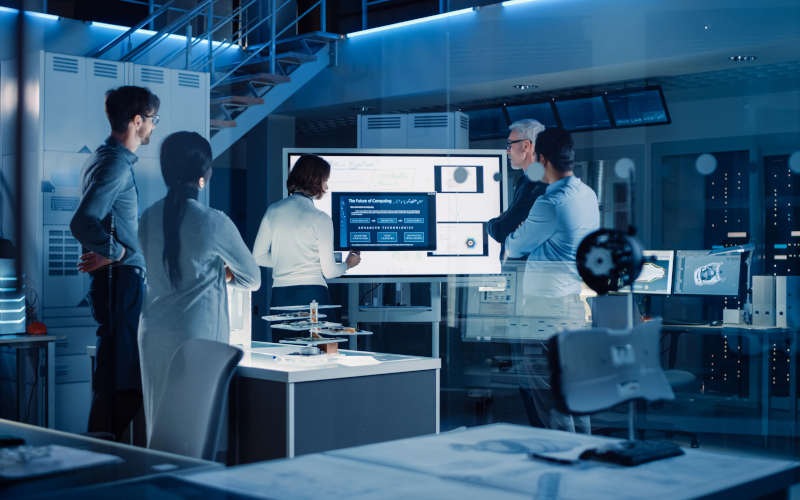
Today, one of the most critical, but least known, procedures in industrial security is the secure development. This article gathers all the best practices for the creation of specific applications and equipment for industrial environments in a secure manner. Security aspects that must take into account both the work done during the design (confidentiality of the company and customers, workers' security...), and the security that the designed product itself must present throughout its life cycle (vulnerability management, access control, input/output management...).
The aim of this article is to address the good practices of secure development, from the perspective of industrial cybersecurity. Although traditional best practices can be applicable to these environments, the fundamental aspects of safety and availability generate different approaches, mainly in aspects related to memory and resource management, update and patch management cycles, etc.
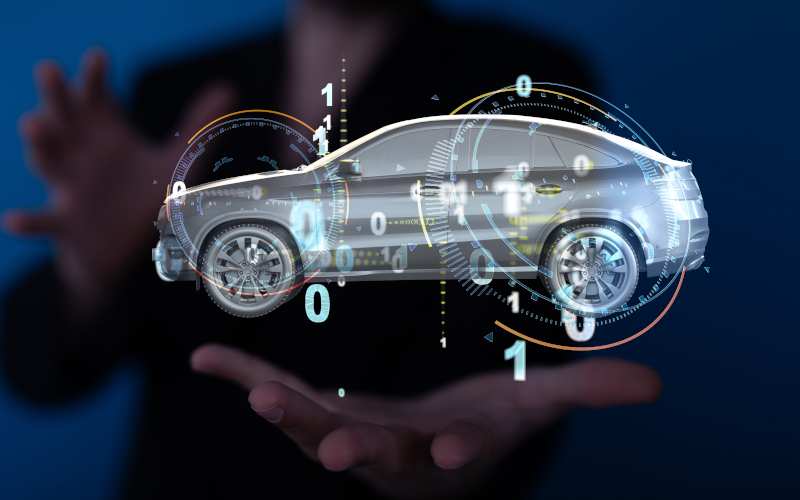
This article aims to present a brief example guide for an implementation of the new standard in a supplier's facilities.
Going through the critical points of the standard, a generic use case will be followed to exemplify how a vehicle manufacturer can adapt its processes to comply with the new standard in an efficient and effective way.
By presenting an overview of the standard and production processes, the aim is to provide a brief guide to serve as a starting point and help avoid common failures in industrial environments when faced with new regulations, such as redundancy of effort, inefficiency in resource management and deficiencies in the application of safety measures.
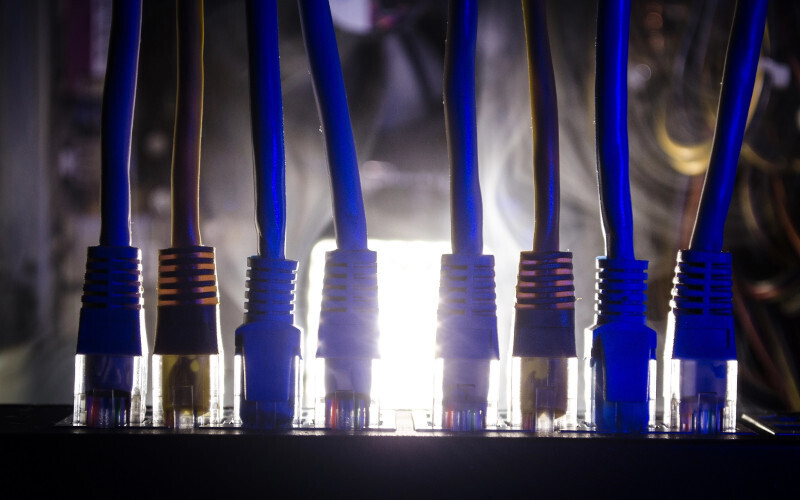
Larger scale and complexity industrial control networks present risks, and cybersecurity needs that usually cannot be met by applying a traditional segmentation model. Factors such as the presence of critical obsolete equipment, equipment managed by third parties or the increased presence of IoT technologies that require external connections, are motivating the adoption of more advanced architectures when applying the principle of defense in depth.
Proper segmentation can be a fundamental aspect in preventing attacks, especially in their propagation to essential and critical production assets. It is also important to adapt to the environment to be segmented. It is a common mistake to try to segment networks based on concepts and schemes like the IT environment.
This article will present some new network models and tips to work on a correct segmentation in an environment where different components are involved (OT, IIoT, IT, IoT).
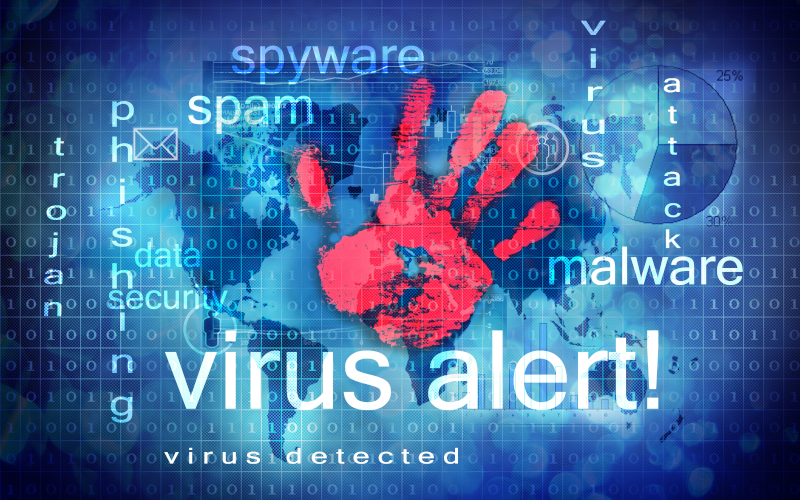
The increasing development of malware targeting the industrial world has not halted its momentum in the slightest. Several research groups have detected a new malware called Fuxnet and are currently investigating its scope. This malware has the capability to send specific requests at the serial level, via RS485/MBus, executing floods to more than 87.000 assets, including control systems and integrated sensors deployed across different sectors. Among the infrastructures compromised by this malware, we find hospitals, airports and other critical infrastructures that provide essential services to the population.
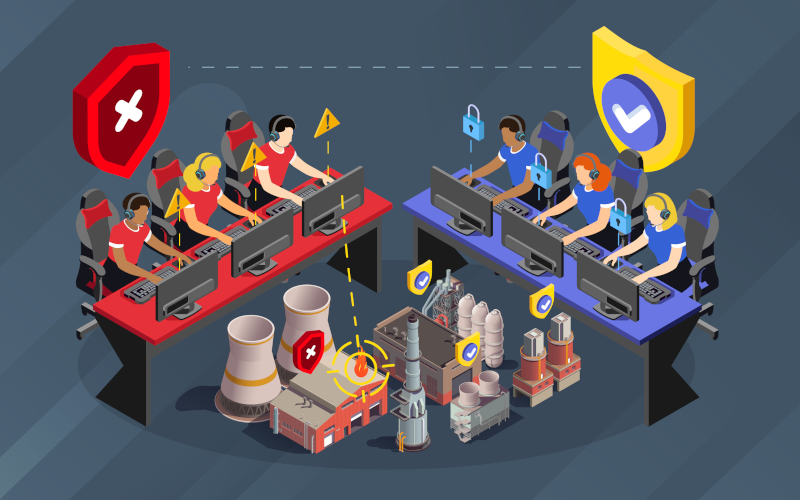
MITRE Caldera OT stands out mainly for being an open-source tool that allows the simulation of different cyber-attacks in industrial environments. This tool was created by MITRE and CISA (US Cybersecurity and Infrastructures Security Agency), as the experts saw the need to be able to improve and understand cybersecurity in industrial environments without using a high number of resources.
In addition, this tool is designed to be used by both the Red Team and the Blue Team, allowing both teams to collaborate with each other to improve the level of cyber security in these environments.